更多干货,请关注资产界研究中心
作者:滕宇
3月23日,国家能源局、国家发改委联合印发《氢能产业发展中长期规划(2021-2035年)》。文中明确提出,氢能是未来国家能源体系的重要组成部分,充分发挥氢能清洁低碳特点,实现绿色低碳转型,将氢能产业作为战略新兴产业和未来重点产业。
此外,《规划》提出了氢能产业发展各阶段目标:到2025年,基本掌握核心技术和制造工艺,燃料电池车辆保有量约5万辆,部署建设一批加氢站,可再生能源制氢量达到10-20万吨/年,实现二氧化碳减排100-200万吨/年。
到2030年,形成较为完备的氢能产业技术创新体系、清洁能源制氢及供应体系,有力支撑碳达峰目标实现。到2035年,形成氢能多元应用生态,可再生能源制氢在终端能源消费中的比例明显提升。
对产业有所了解的朋友们应该知道,自2016年氢能产业纳入国家能源战略以来,我国氢能产业高速发展,在产业链各环节已初具雏形,完成了从0-1的过程、正在迈向从1-N的道路。
根据中国氢能联盟的预计,2020年至2025年间,中国氢能产业产值将达1万亿元,2026年至2035年产值达到5万亿元。可以说,氢能未来的前景就是星辰大海。
当然,现阶段产业链各技术环节仍旧存在着诸多需要攻关的技术,比如液态氢储运,IV型储氢瓶,大型加氢站、电堆成本等等。
储量上来看,氢是宇宙中含量最多的元素,大约占据宇宙质量的75%,地球上丰富的水资源中蕴含着大量可供开发的氢能,未来是获取最便利和成本最低的能源之一。
电池生产过程中要使用大量锂、钴、镍等金属材料,其生产过程中,金属材料的开采、生产加工都会产生大量能量消耗和碳排放,属于冶炼、化工产业。
而氢气直接燃烧或通过燃料电池发电的产物为水,能够实现真正的零碳排放,对环境不造成任何污染。故而氢能被称为终极能源。
按照产业链由上到下的次序,氢能源产业链可以分成三段,上游是氢生产与供应;中游,是燃料电池及核心零部件,而它的下游,则是燃料电池应用。
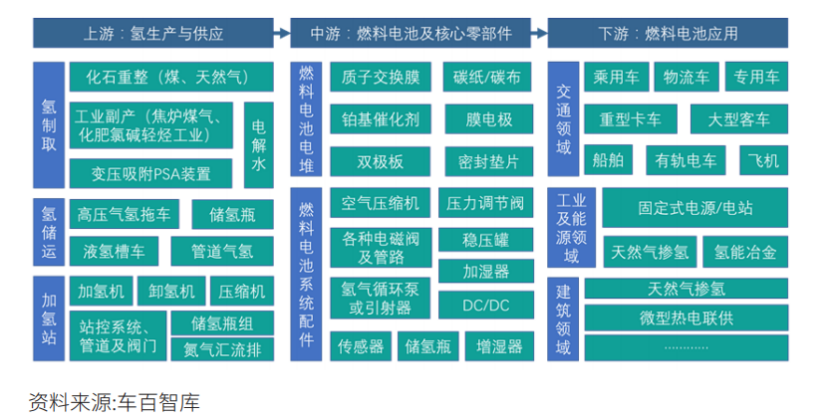
现阶段较为成熟的制氢的技术路线有三种:一是以煤炭、天然气为代表的化石能源重整制氢,俗称蓝氢;二是以焦炉煤气、氯碱尾气、丙烷脱氢为代表的工业副产气制氢,俗称灰氢;三是电解水制氢,俗称绿氢。
前两者生产氢气的技术无法摆脱对传统能源的消耗,虽然通过碳捕捉与封存技术(CCS)可有效降低化石能源制氢过程中产生的碳排放。但长期来看,只有可再生能源电解水制备的“绿氢”才能实现真正的零碳排放。
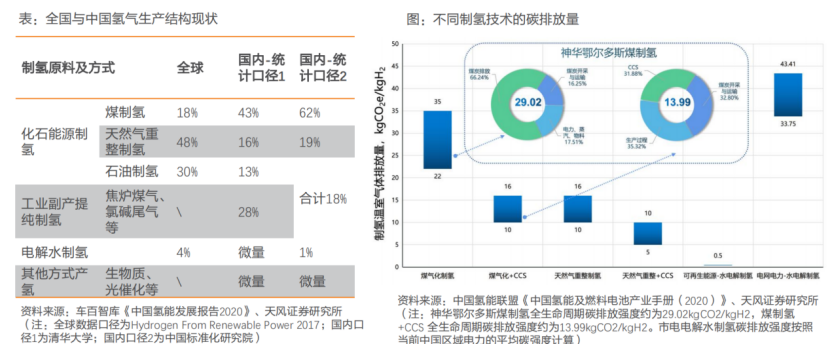
我国是世界上最大的制氢国,年制氢产量约3300万吨,其中,能达到工业氢气质量标准的约有1200万吨。可再生能源装机量全球第一,在清洁低碳的氢能供给上具有巨大潜力。
在未来,通过电解水可以将富足的可再生能源转化成绿氢,为建筑、交通、工业等高排放部门供给清洁环保的绿色原料和燃料,从而减少化石能源的使用,有效减少碳排放。
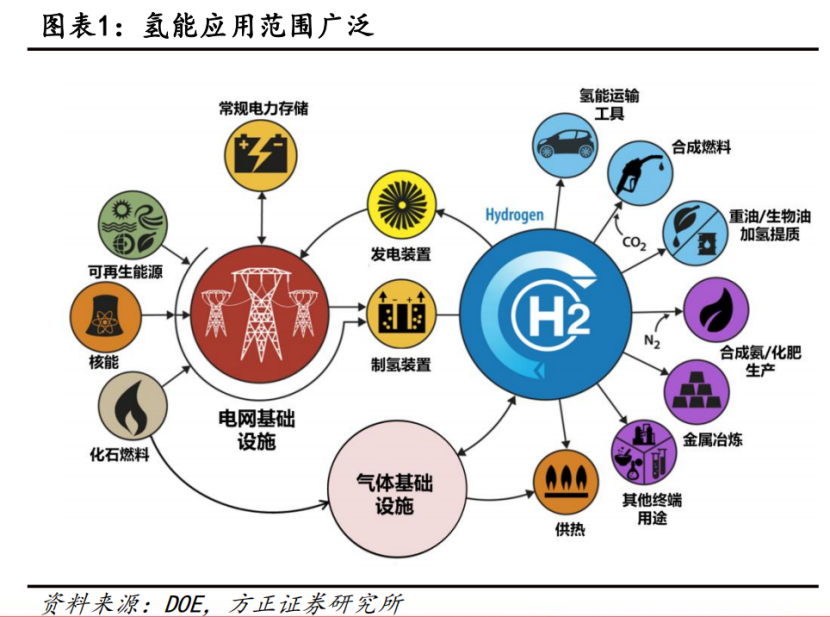
不过,实际进展道阻且长。根据IRENA的测算,全球仅有4%的氢气来自电解水制氢,其余均来自煤炭、天然气以及石油炼化领域。
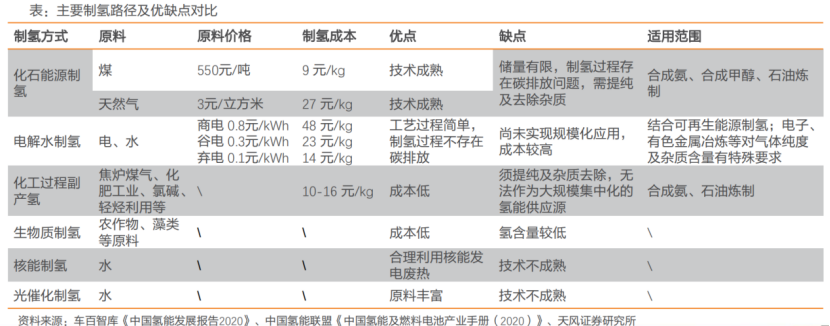
然而随着光伏、风电的进一步降本,到2030年国内部分可再生资源优势区域,其度电成本到达到0.1-0.15元/KWh,绿氢成本逐步下降到14元/KG左右,实现与灰氢平价。
02 PEM电解水技术
电解水制氢的基本原理,是水分子在直流电作用下解离生成氧气和氢气,分别从电解槽的阳极和阴极析出,具体可分为碱性水电解、质子交换膜水电解(PEM)、阴离子交换膜水电解(AEM)以及固体氧化物水电解(SOE)四种技术路线。
由于是碱性条件,因此可以使用非贵金属电催化剂,因此电解槽造价成本较低;但是,难以快速启动和变载,无法快速调节制氢速度,因此与可再生能源适配性较差。
从技术角度看,PEM电解水技术具有独特优势,许多新建项目开始转向选择PEM电解技术,近年开始获得较多的市场份额。
相较碱性电解水技术,PEM电解采用纯水电解,无污染、无腐蚀;其次,质子交换膜拥有更高的质子传导性,电解槽工作电流可大大提高,从而提升电解效率。
同时PEM电解水技术能够提供更宽的负载范围和更短的响应启动时间,与水电、风电、光伏(发电的波动性和随机性较大)具有良好的匹配性,最适合未来能源结构的发展。
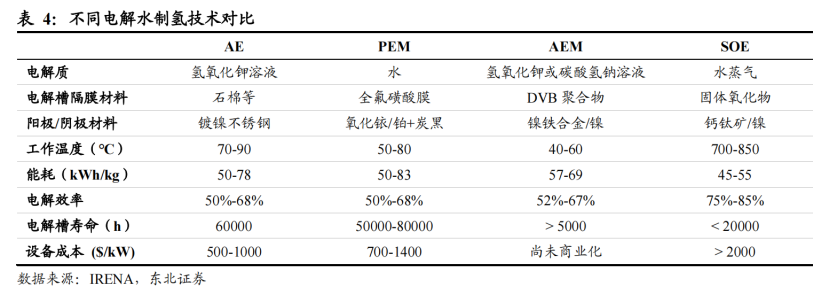
2015年,西门子和林德气体在德国美因茨能源园区建成当时世界最大PEM电解工厂,额定装机功率达6MW,此后PEM电解项目数量和装机规模也在不断提升。2020年,法液空完成在加拿大贝坎库尔的20兆瓦PEM电解水项目建设。
2021年3月4日,上海电气电站集团与中科院大连化学物理研究所正式签订“兆瓦级模块化高效PEM电解水制氢设备及系统开发项目合作协议”。
2021年3月18日,阳光电源重磅发布了“SEP50”PEM电解槽。据了解,该产品单槽功率250kW,是国内目前单槽功率最大的PEM电解槽,也是国内首款量产的50标方PEM电解槽。
2022年1月15日,龙蟠科技(603906.SH)全资子公司龙蟠氢能源公司与中国科学院大连化学物理研究所共同启动PEM电解水制氢催化剂的研发项目。
可以看出来,国内PEM电解项目规模较小,当前国内交付应用的设备大多是小型电解槽。到底是什么因素制约着PEM电解制氢的推广呢?逐本溯源,我们需要回到PEM电解槽的构造上。
其中扩散层、催化层与质子交换膜组成膜电极,是整个水电解槽物料传输以及电化学反应的主场所,膜电极特性与结构直接影响PEM水电解槽的性能和寿命。
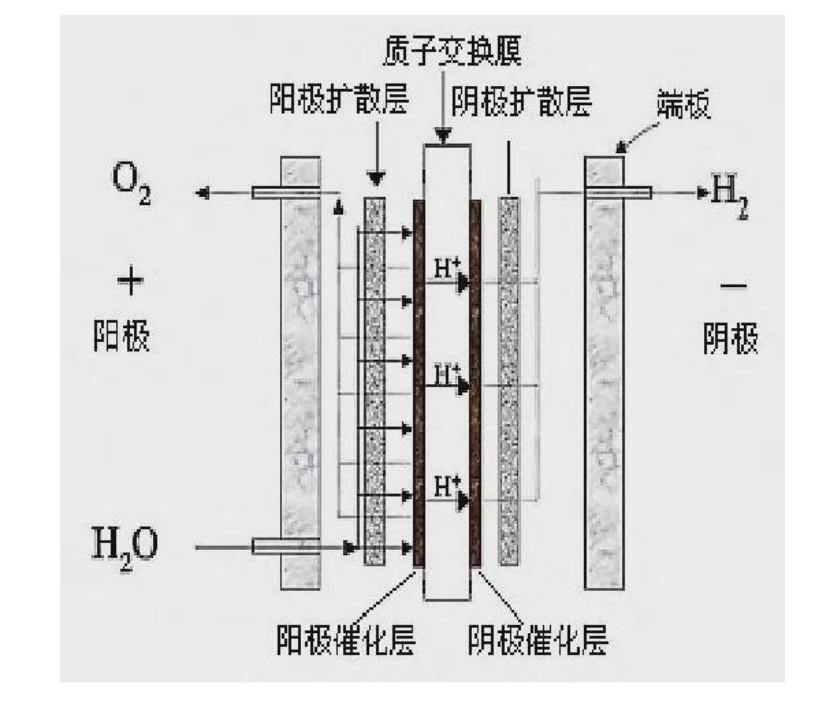
在投资成本方面,过去5年电解槽成本已下降了40%,但是目前PEM电解成本投入仍旧比碱性电解水至少多一倍。投资和运行成本仍然是PEM水电解制氢亟待解决的主要问题。
而质子交换膜是电解槽的核心部分,不仅传导质子,隔离氢气和氧气,而且还为催化剂提供支撑,其性能的好坏直接决定水电解槽的性能和使用寿命,因此在整个设备中至关重要。
区别于碱性水电解制氢,PEM水电解制氢选用具有良好化学稳定性、质子传导性、气体分离性的全氟磺酸质子交换膜作为固体电解质替代石棉膜,能有效阻止电子传递,提高电解槽安全性。
质子交换膜制备曾长期被杜邦、戈尔等美国和日本少数厂家垄断,目前主要使用杜邦的nafion-711和511系列。该系列主要采用全氟磺酸树脂制造,膜厚度是普通燃料电池交换膜的10-15倍,因此整体成本非常高。
目前,国内东岳、科润等企业正积极布局,东岳150万平米质子交换膜生产线一期工程已投产,科润100万平米质子交换膜项目也已开工。随着国内技术的不断突破,国产质子交换膜实现进口替代的空间巨大。
可是,从上游资源的分布来看,这两种贵金属在国内的储量非常少,主要分布在南非、俄罗斯、南美等地区,一旦PEM制氢大规模使用,国内产业就会面临原材料极度依赖外国进口的供应链风险。
与此同时,国内这两种催化剂的制作工艺和产能水平还无法与JohnsonMatthey等外资品牌媲美,国内PEM设备企业进口铂和铱催化剂的需求仍比较明显。
扩散层材料方面,目前行业内主要使用烧结毡、钛毡和碳毡等材料路线,其中阳极以钛毡效果最高,阴极主要使用碳毡,为了实现材料与自家工艺的最佳配合,扩散层填充材料基本上都是需要定制,这也是体现各家工艺水平的核心环节之一。
除了扩散层阳极填充材料,双极板、端板等零部件都是使用钛合金材料以防止发生氢脆现象,提高设备整体的安全性。钛合金难加工,对国产企业的加工精度水平也提出非常高的要求。
然而,在未来能源版图中,氢能无疑是一块重要拼图,在国家积极推动和资本介入下,实现国产化替代的前景较为乐观。
注:文章为作者独立观点,不代表资产界立场。
题图来自 Pexels,基于 CC0 协议
本文由“阿尔法工场”投稿资产界,并经资产界编辑发布。版权归原作者所有,未经授权,请勿转载,谢谢!
原标题: 推开万亿氢能赛道的第一重门